The importance of new manufacturing processes and in particular additive manufacturing is increasing due to the economic and technological advantages even in safety-critical and demanding fields of application, such as energy generation and conversion.
While in the past such processes were only used for the production of prototypes, functional samples, and, if necessary, spare parts, they are increasingly considered as valid manufacturing technologies already in the development process of high-performance components. This allows specific advantages to be realized, such as higher operating temperatures due to cooling channels close to the surface in the case of turbine blades and geometric compaction of complex valve geometries.
In addition to additive manufacturing in powder bed with LPBF/SLM, DED/WAAM processes as well as the application of new joining processes, such as electron beam welding, narrow gap welding, cold gas spraying, and hot isostatic pressing, will be the focus of this workshop.
The workshop will look at the manufacturing processes, the resulting material properties that can be achieved, the proof of structural integrity especially for the challenging operating environments, such as corrosion, creep resistance, and fatigue. In addition, suitable in-process and post-process quality assurance methods will be addressed.
- Advanced Manufacturing for powerplants and safety-relevant parts
- DED/WAAM additive manufacturing
- Structural integrity of AM
- LM additive manufacturing
- New materials
- Electron beam welding and narrow gap welding
- Cold gas spraying
- Form generating HIP
- Quality assurance and NDT
Program (times correspond to CEST)
Abstracts
Author: Potzernheim-Zenkel, Christian – Voestalpine
Additive Manufacturing of hybrid structures is one of the main focus topics of voestalpine´s Metal Forming Division. With the combination of classic forming technologies like stamping and bending with material deposition technologies, we break new ground in manufacturing structural parts. For example we will show new approaches on crash-structures by combining Laser-Metal Deposition (LMD) and Wire+Arc Additive Manufacturing (WAAM) with pre-formed B-Pillars. First tests show promising results including a significant weight reduction. This new manufacturing technologies open the ways to build parts with the weight of a few grams up to several tons.
Author: Beckers, Daniel - Rosswag-Engineering
Additive manufacturing, with its advantages regarding the viability of complex geometries, can provide tremendous values in the areas of reactors, energy generation and heat exchangers. In order to be able to guarantee process-safe operation, a large number of factors must be taken into account during the production of the necessary parts. To ensure this quality and safety, the generation of metal powder and qualification of AM parts under the pressure equipment directive are going to be presented and the main working steps for the certification will be outlined.
Author: Brotsack, Markus – Impact-Innovations GmbH
Cold spray (CS) technology is a well-established technique for metallic deposits in various industries. CS process is known to deposit the powder particles in solid-state far below the melting point of the materials; as a result, common problems associated with temperatures, such as high-temperature oxidation, thermal stresses, and phase-transformation, can be avoided. Moreover, cold spray offers short production times, unlimited component size capability, and flexibility for localized deposition. Present work demonstrates the main properties of cold spray process, as well as the properties of wear and corrosion resistant coatings. Further developments are shown where cold spray technology is used for building up 3D parts mainly used in aerospace industry for combustion chambers and rocket nozzles for example.
Author: Kallee, Stephan - Alustir
Linear Friction Welding is particularly suitable for manufacturing blisks (bladed discs) for aero-engines and for producing making-near netshape fuselage parts. One of the best-kept secrets of high-quality linear friction welding is that the frequency is kept constant, while the amplitude is reduced to zero at the end of each weld. The presentation will thus focus on:
-
- Principle
- Linear Motion
- LFW Machines
- Friction Welding Variants
- Design
- Quality Control
Author: Woy, Udisien - Nuclear Advanced Manufacturing Research Centre (Nuclear AMRC) University of Sheffield
Advanced manufacturing technology (AMT) options are required for processing high heat flux (HHF) components used in power plant. However, the introduction of advanced technologies aptly necessitates the development of both candidate materials and advanced manufacturing processes, in order to demonstrate compliance with or equivalence to existing codes and standards. Additive manufacturing (AM) is an AMT of significant interest, due to the potential prospects for legacy and future HHF applications. These important developmental perspectives are explored via the ongoing SafeG and NUCOBAM EU H2020 projects. Distinctly, the goal of NUCOBAM is to advance the use of AM in the nuclear industry by facilitating the implementation of nuclear design codes and standards for AM, while SafeG focusses on advancing research and development of gas-cooled fast reactors (GFR) by reviewing material and technology options to enhance the safety of the GFR demonstrator ALLEGRO. Correspondingly the principal aim is to demonstrate the efficacy of different AM techniques, including LPBF and DED processes, which have been selected to underpin the development of designated HHT materials, and specific part qualification procedures.
Author: Hermann, Florian - Trumpf
Additive manufacturing with aluminum alloys has a great potential to meet the growing demand for lightweight construction and flexibility. However, higher build rates and higher process efficiency are necessary for laser metal deposition (LMD) to be more economically competitive. The so called high-speed LMD allows high build rates by partial melting of the powder before it hits the melt pool but is currently limited to coatings of rotationally symmetrical parts. Our goal is to apply this process technology to the additive manufacturing of AlSi10Mg and thereby increase the build rate.
Author: Yoo, Mark - US Nuclear Regulatory Commission
The Nuclear Regulatory Commission (NRC) is preparing for industry use of advanced manufacturing technologies (AMTs) to fabricate components both for new plant construction and repair and replacement in operating plants. The NRC has adopted a proactive engagement strategy to identify any technical or regulatory issues early in the development of advanced manufacturing technologies in an effort to expedite NRC’s acceptance of these technologies. The NRC has completed its initial set of technical and regulatory actions as outlined in Revision 1 of the NRC’s AMT Action Plan. The initial focus, based upon industry interest and the potential for near-term application, has been on laser-powder bed fusion, laser-directed energy deposition, cold spray, electron beam welding, and powder metallurgy-hot isostatic pressing. The NRC has identified and initiated its next phase of technical preparedness, regulatory preparedness, and communications and knowledge management activities to continue to prepare for industry implementation of AMTs.
Author: Ravi Narayan, Lakshmi - University of Connecticut
An understanding of solidification cracking during rapid solidification processing is sought so that alloys can be developed for defect-free additive manufacturing. Experimental methods are described, that provide insight into the susceptibility of an alloy to crack, and which are also inputs to models that aim to predict cracking. To determine microsegregation during rapid solidification, laser-glazing experiments were combined with TEM and EDS. Available rapid solidification theories were compared with these experimental results. To determine the thermal gradient in the melt pool, optical measurements were made in-situ during laser-glazing.
Author: Wright, Richard - Idaho National Laboratory
Section III, Division 5 of the American Society of Mechanical Engineers Boiler and Pressure Vessel Code covers construction rules for elevated-temperature nuclear components. Microreactor developers have expressed a need for advanced manufacturing processes to fabricate microreactor components to reduce manufacturing costs. Components fabricated using manufacturing processes other than conventional techniques are not currently qualified in Section III, Division 5. An expeditious approach to qualifying an advanced manufacturing process for alloys whose wrought-product form is already qualified in Division 5 is to demonstrate the resultant properties from the advanced manufacturing process are equivalent or superior to the wrought-product form. Powder metallurgy-hot isostatic pressing (PM-HIP) is a mature technology that offers many advantages that are attractive to the microreactor industry. Preliminary data show that the elevated-temperature creep-fatigue properties of PM-HIP 316H stainless steel (SS) are reduced compared to the Wrought 316H SS, which is qualified in Section III, Division 5. Work is ongoing to identify the mechanisms responsible for the reduced creep-fatigue properties and to establish acceptance criteria to confirm the adequacy of the component for service.
Fees and conditions of participation
The workshop "Advanced Manufactured Components for Safety Relevant Applications" is an online workshop. After your binding registration we will send you a link to the conference platform in a timely manner.
The conference fee includes the access to the lecture-videos (video-on-demand) and the pdf-files of the presentations (a few days after the workshop) on the conference plattform for 14 days.
The event language is English.
Fees
€ 120,- Day Ticket
free Speaker
free Students (with ID)
Registration
Please fill in the following fields:
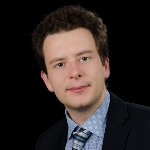
Martin Werz
Dr.-Ing.Abteilungsleiter
- Profil-Seite
- +49 711 685 62597
- E-Mail schreiben
- Abteilung Fügetechnik und Additive Fertigung